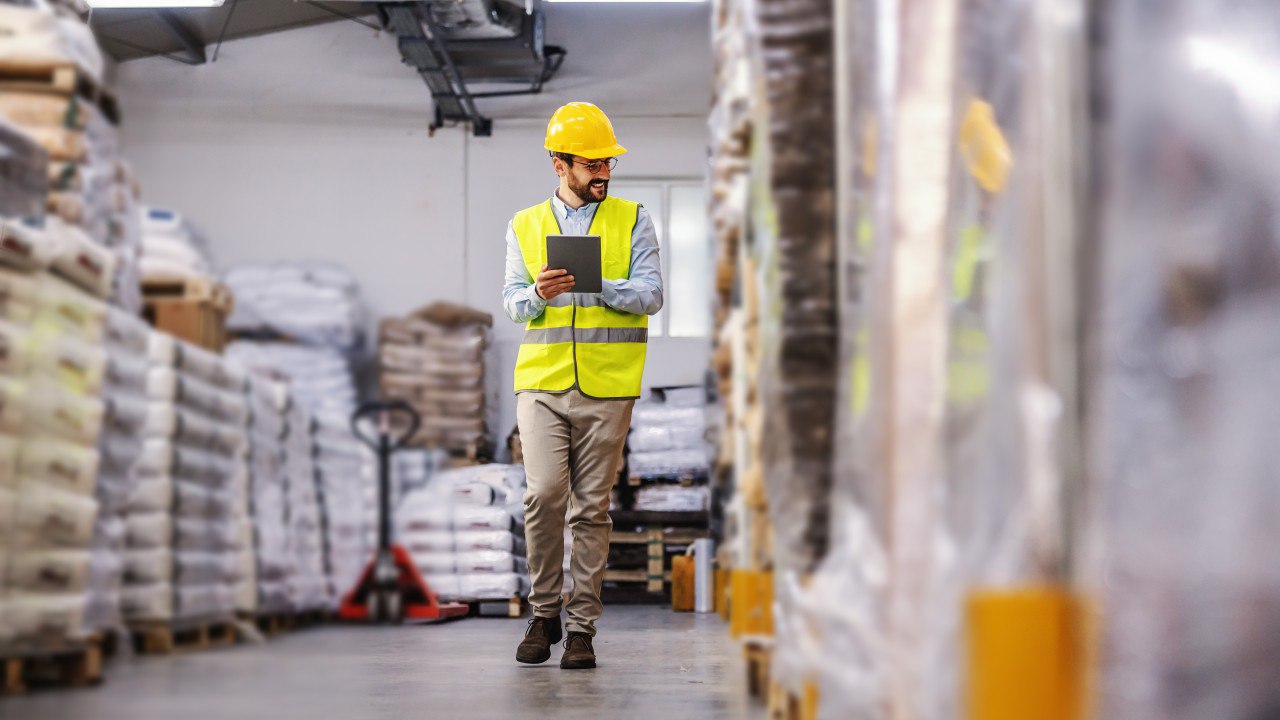
Why Are So Many Warehouse Teams Still Using Paper in 2025?
Walk into a warehouse in 2025, and you’re likely to find something that feels a little out of place: clipboards.
Despite advances in warehouse management software, real-time scanning, and mobile logistics tools, many warehouses still rely on printed pick tickets, hand-written inventory notes, and paper-based workflows. In a world obsessed with automation and optimization, it’s a surprising reality.
But when you dig a little deeper, it makes sense.
The Persistence of Paper
Paper is familiar. It’s cheap. It doesn’t crash, doesn’t need charging, and it doesn’t require training. For many warehouse teams, especially in small to midsize operations, paper has simply worked for decades.
It’s easy to pass along, easy to mark up, and—at least on the surface—simple to manage. Managers often know where to find things: on someone’s desk, attached to a pallet, or clipped to the wall.
So when the conversation turns to digitization, the first reaction is often: Why fix what isn’t broken?
But that question hides a deeper issue.
What Paper Doesn’t Show You
Paper might feel safe, but it hides problems. It can’t track who moved a part. It won’t alert you when inventory is misplaced or miscounted. And it certainly won’t back itself up.
Over time, warehouses that rely heavily on paper encounter challenges like:
Lost pick tickets or handwritten notes that result in shipping delays.
- No audit trail—making it hard to identify when and where mistakes were made.
- Slow training for new employees, who have to learn tribal knowledge from scratch.
- Errors in transcription, especially when handwriting is unclear or tasks are duplicated.
In the moment, these issues feel like minor hiccups. But over time, they add up to lost hours, higher costs, and frustrated teams.
The Real Cost of Comfort
One of the biggest reasons paper survives in warehouses is inertia. Change feels risky. Teams are stretched thin already, and introducing new technology sounds like just another headache.
Plus, there’s a valid fear: What if the new system is harder to use than what we have now?
That fear isn’t unfounded. Many legacy software systems in the warehousing space were built with complexity in mind—systems so bloated and unintuitive that training takes weeks, and teams never fully adopt the tools.
So instead of risking a failed transition, companies stick with what they know.
But over time, that comfort becomes expensive:
- Repetitive manual tasks drain labor hours.
- Small mistakes lead to customer chargebacks or lost clients.
- Lack of visibility makes it hard to scale or optimize.
And perhaps most importantly, it’s difficult to grow when you can’t measure what’s really happening inside your operation.
What’s Changing in 2025?
The shift away from paper isn’t being driven by software companies—it’s being driven by customer expectations.
Warehouses are now expected to:
- Offer real-time status updates
- Shorten fulfillment windows
- Handle more SKUs with greater accuracy
These are difficult demands to meet with pen and paper.
As e-commerce continues to rise, and more brands rely on third-party logistics (3PL) partners, the pressure for transparency and accountability increases. The ability to say, “Here’s who scanned it, where it was stored, and when it was shipped,” is no longer a bonus—it’s a baseline.
In 2025, even small and mid-sized warehouses are beginning to look for lightweight, easyto - deploy tools that give them digital visibility—without slowing them down. It’s not about “going paperless” for the sake of it. It’s about regaining control of your data and processes in a fast-moving industry.
What Digitization Can Look Like
Going digital doesn’t have to mean massive disruption. In fact, some of the most successful transitions happen in stages.
Here’s what that might look like:
- Start with part and location spreadsheets. You probably already have them—now make sure they’re structured and up to date.
- Track user actions. Add simple accountability features—knowing who completed a task can eliminate guesswork.
- Track user actions. Add simple accountability features—knowing who completed a task can eliminate guesswork.
- Use barcodes. Label bins and shelves with scannable codes to reduce human error during picks and putaways.
- Choose intuitive software. Avoid overly complex systems. If your team can’t learn it in a week, it’s not going to stick.
The most important thing? Let the floor team lead the way. If they find value in the new system, adoption will follow.
Paper’s Not the Enemy—But It Has a Shelf Life
To be clear: paper isn’t evil. It’s familiar, flexible, and it still has a role to play in some operations.
But it can no longer be the backbone of your warehouse if you want to grow, compete, or modernize.
The warehouses that succeed in the next five years won’t be the ones with the most automation—they’ll be the ones with the clearest view of what’s happening inside their four walls.
And that starts with visibility.
Have thoughts on this? We’d love to hear how your team is handling the shift from paper to digital. Leave a comment, share your story, or email us at customersupport@3gistics.com.
Try now 3gistics to discover logistics that are efficient, effective, and customized to your needs.